In the world of manufacturing and production, bonding solutions play a crucial role in joining materials together. From assembling components to sealing packages, the right adhesive or sealant can make all the difference in ensuring product quality, durability, and safety.
Understanding Adhesives
Adhesives are substances used to join two or more materials together by creating a strong, lasting bond between their surfaces. They come in different forms, such as liquids, pastes, or solids, and meet specific requirements based on the materials being bonded and the intended application.
Types of Adhesives
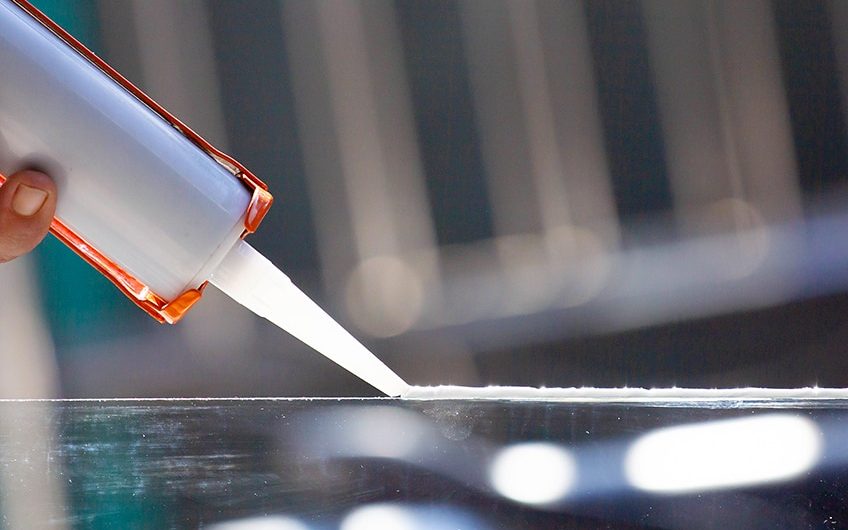
- Structural adhesives ─ These adhesives are designed for high-strength, load-bearing applications. These adhesives find frequent applications in industries such as construction, transportation, and aerospace for bonding materials like metals, composites, and plastics. Examples include epoxy, acrylic, and polyurethane adhesives.
- Pressure-sensitive adhesives ─ These adhesives form a bond with minimal pressure and remain tacky at room temperature. Manufacturers commonly use them in tapes, labels, and protective films. Examples include rubber-based and acrylic adhesives.
- Hot melt adhesives ─ The experts at Trecora explain that hot melt adhesives are solid at room temperature but become liquid when heated, allowing for fast and efficient bonding. Industries widely use hot melt adhesives in packaging, woodworking, and product assembly. Examples include ethylene-vinyl acetate (EVA) and polyamide-based hot melt adhesives.
- Reactive adhesives ─ These adhesives undergo a chemical reaction during the bonding process, resulting in a strong, durable bond. Industries often use them in automotive, aerospace, and construction applications. Examples include epoxy, polyurethane, and silicone adhesives.
Understanding Sealants
Sealants are materials used to fill gaps or joints between surfaces, preventing the passage of liquids, gasses, or solids. They are often used for weatherproofing, insulation, and protecting against environmental factors.
Types of Sealants
- Silicone sealants ─ These sealants are highly flexible, durable, and resistant to moisture and temperature extremes. Construction, automotive, and aerospace industries commonly use these sealants for sealing joints and gaps.
- Polyurethane sealants ─ These sealants are known for their excellent adhesion, flexibility, and resistance to chemicals and abrasion. The construction, marine, and transportation industries widely use polyurethane sealants for sealing and bonding applications.
- Acrylic sealants ─ These sealants are easy to apply, paintable, and have good flexibility and adhesion. Construction and glazing applications commonly use them to seal windows, doors, and other openings.
- Butyl sealants ─ These sealants are highly resistant to moisture, weathering, and aging. Construction and automotive industries often use these sealants for sealing joints and lap seams.
Factors to Consider
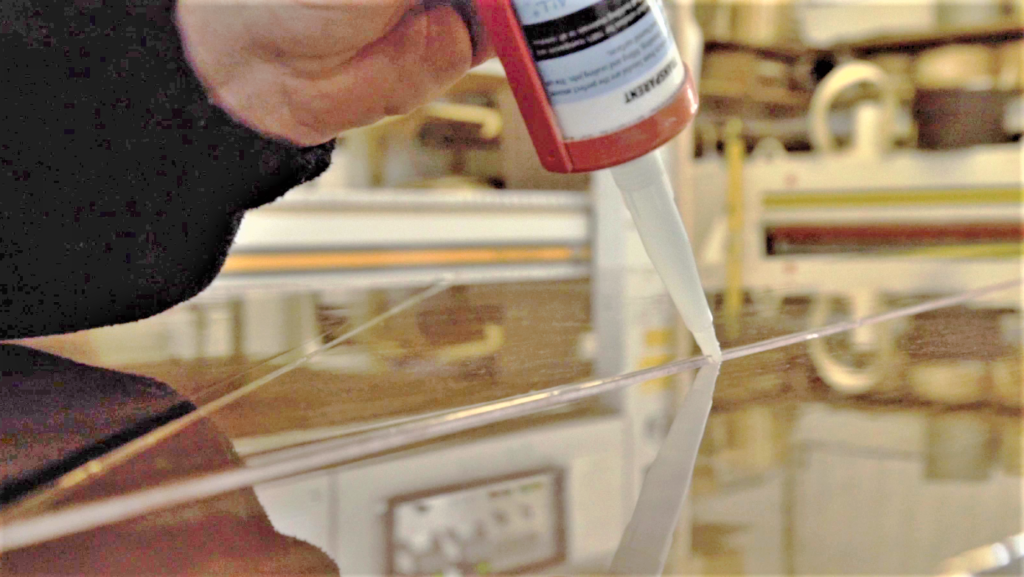
When selecting an industrial bonding solution, several factors should be considered:
- Substrate compatibility ─ Different adhesives and sealants are designed for specific materials, such as metals, plastics, glass, or concrete. Ensuring compatibility is crucial for achieving a strong, lasting bond.
- Environmental conditions ─ Factors like temperature, humidity, and exposure to chemicals or UV radiation can affect the performance of adhesives and sealants. Choosing a solution that can withstand the intended operating conditions is essential.
- Application requirements ─ Consider factors like curing time, viscosity, gap-filling capability, and whether the application requires a flexible or rigid bond.
- Regulatory compliance ─ Certain industries, such as food and beverage or medical, may have specific regulations regarding the use of adhesives and sealants. Choosing a compliant solution is crucial.
- Cost and efficiency─ Consider the overall cost, ease of application, and productivity when selecting an industrial bonding solution.
Conclusion
The right industrial bonding solution can not only improve the performance and longevity of products but also streamline manufacturing processes and increase overall productivity. As technology continues to evolve, it’s likely that new and innovative bonding solutions will emerge, offering enhanced capabilities and addressing emerging challenges.
Staying up to date with the latest developments and industry best practices means manufacturers can remain competitive and deliver superior products that meet the highest standards of quality and durability.